There are 4 different types of board:
(1) Plywood: layers of wood laid down in alternate directions
and glued together
(2) Strip-core boards: timber laths glued together in
rows and sandwiched between outer veneers
(3) Particle boards: wood chips are glued and compressed.
These boardsmay be veneered, covered with a plastic laminate
or left plain.
(4) Fibre boards: wood fibres are mixed with glue, they
are then heat and pressure treated to form boards of different
densities. Again, these boards may be veneered or left plain.
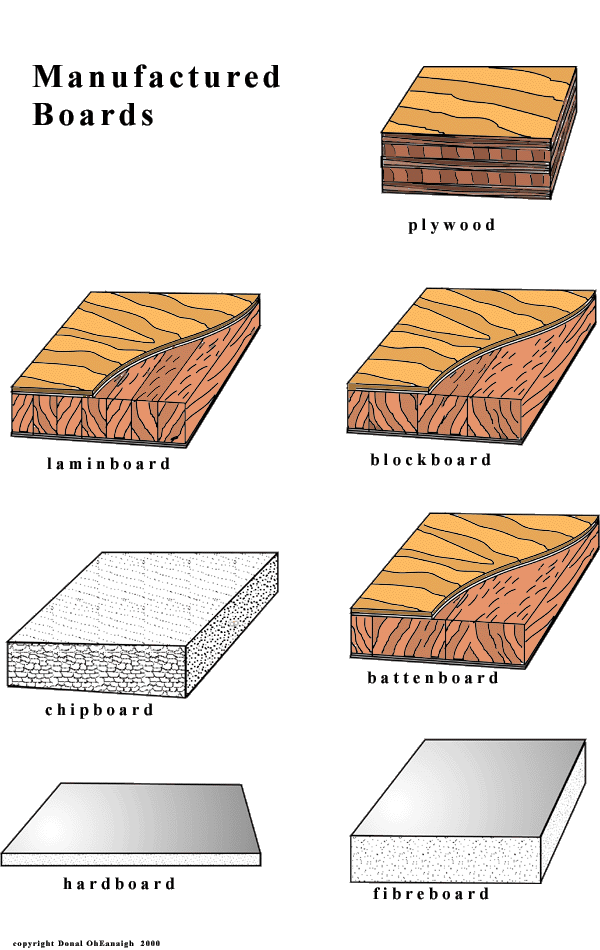
Plywood
Veneers are thin sheets of wood cut from the surface of a log.
In plywood each veneer is laid at 90 degrees to the veneer above
and below it This prevents shrinkage and also makes the board
strong as it cannot split along the grain. A plywood board must
have an uneven number of layers (3,5,7,9 etc.,) in order that
it be "balanced". The grain on the two outside layers
must be run in the same direction or else the board will warp.
There are 3 kinds of plywood: Three-ply (made up of 3 veneers
of equal thickness); Multi-ply (made of more than 3 veneers making
the board stronger but also more expensive) ; Stoutheart (a thick
centre veneer sandwiched between 2 thin outer veneers).
There are 2 grades of plywood : Interior
grade (used only indoors, neither the veneers nor the casein
glue would withstand the weather) ; Exterior grade (the
veneers used are naturally durable timbers, the glue used is
urea formaldehyde. These plywoods are W. B. P. that is, water
and boil proof.
Strip-core boards
These boards are made up of strips or laths of timber (either
a cheap hardwood or a softwood) all running with their grain
in the same direction. Thick veneers are bonded to the strip
core with their grain running at 90 degrees to the grain of the
strips. This makes the board strong in the same way as plywood.
There are 3 types of strip-core board which depends on the thickness
of the timber laths: batten board, block board
and lamin board.
The main advantage of strip-core boards over plywood is that
you can screw and nail into the edge.
Particle boards
These boards are made by taking wood chips whkh have been graded
(sieved to the same size) and mixing with a synthetic resin glue.
The wood chip used is a by-product of sawmills which helps in
the conservation of trees. Sawdust from workshops and mills is
also used on the outer layers of the board to give it a smoother
finish. These boards can be covered with a plastic laminate for
use as kitchen worktops etc., or they can be veneered for use
in the manufacture of furniture.
Fibreboards
Fibreboards are made by mixing wood-pulp or fibres with synthetic
adhesives. The boards are heat-treated to about 200 degrees C
and placed in a press to make a dense material. Hardboard is
uniformly dense throughout, being rough on one side and smooth
on the other. Medium density fibreboard has outer layers that
are very hard with a slightly softer inner core. Fibreboards
can have other substances added at the mixing stage in order
to give them particular qualities, for instance to make them
fire-resistant or water-resistant
Sizes of Boards
Most timber sheet material comes in standard 8ft x 4ft (2440mm
x 1220mm) sheets Smaller and larger sized panels are also available.
Typical thicknesses for sheet material are: 3mm, 4mm, 6mm, 9mm,
l2mm, 18mm and 25mm.
Sheet Storage
Sheet materials must be stored flat and in a dry place up off
the ground. If not boards can warp or get damp. |